基于计算机辅助设计技术(TCAD)的工艺开发
随着半导体工艺开发和制造成本的快速上升和复杂程度不断加深,半导体制造商如今面临着前所未有的挑战。为了满足成本更低和功能更多的产品需求,半导体工艺的更新换代取决于不同器件类型的升级和集成——核心逻辑金属-氧场效晶体管(MOSFETs),嵌入式闪存,高压器件等——需要对制造设备和晶圆试验测试进行巨额投资才能实现工艺目标。而且,一旦新工艺投入制造,尽快实现制造良品率达到尽可能高的水平则变得越来越重要,甚至要保证采用新工艺制造的产品的获利能力。
本文引用地址:https://www.eepw.com.cn/article/202500.htm为帮助减轻这些挑战,东芝已经开发出基于模拟的技术实现良率的快速提升,并减少工艺开发成本和时间。该方法在技术生命周期的各个阶段,从开发到制造,都依赖工艺和器件模拟软件的应用,即计算机辅助设计技术(TCAD)。这种技术适用性强,可以应用到其它半导体制造环境当中。
方法描述
计算机辅助设计技术(TCAD)方法依赖于特征尺度形貌模拟器Sentaurus Topography和硅工艺模拟器Sentaurus Process,其中包括三个阶段。
1. 工艺开发概念的设计和选择
2. 概念选择
3. 对批量生产进行工艺优化
开发工艺流程的第一阶段是对开发概念的设计和制定,移除无效工艺步骤和失效(或危险)的晶格。确认这些“危险晶格”对建立一个初始工艺流程至关重要,并为进一步优化打下坚实的基础。
这个确认过程是通过使用工艺模拟工具二维器件形状(Device D-2)来完成的,横截面形状通过形貌模拟器进行模拟,温度步骤如扩散和氧化过程则由工艺模拟器来完成。一旦整个工艺的轮廓制定完成,代表晶格被移除并核对,对这些晶格的横截面视图是否存在故障进行检查。
下一步骤开始进行晶圆测试,并对物理模型进行校准。对工艺流程变量进行优化,使该流程可以更适应制造过程中出现的变化。在最后阶段投入批量生产时,工艺流程的重点再次回到使用从生产环节获得的质量控制数据进行模拟,这些数据包括蚀刻速率、沉积率、氧化条件等,这些将被作为模拟器的输入数据。
通过这个方法,结合移除所谓的危险晶格,以及容易导致故障的工艺,减少检验工艺流程所需要的试验分裂条件数量,可以明显地减少开发时间,同时提供更适用的工艺进行批量生产。其结果就是:优化良率。
开发和制造阶段
图1为第一阶段移除危险工艺步骤和晶格。首先,用户确定获得横截面视图的位置。如A-A’或E-E’。
器件版图(左上图)及对其不同横截面进行分析(右侧)。底部为工艺流程。
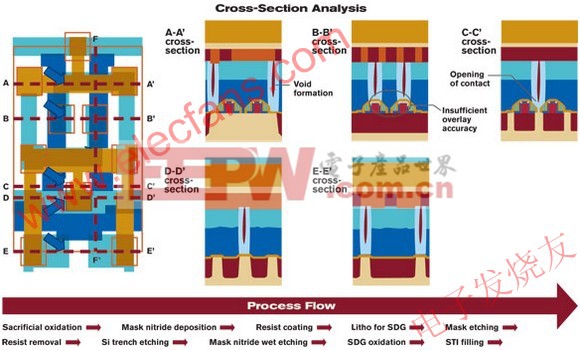
图1.器件版图(左上图)及对其不同横截面进行分析(右侧)。底部为工艺流程。
在给定工艺流程和所选择位置使用计算机辅助设计技术(TCAD)工具,通过观测检查每个晶格模拟结果的不同横截面视图。例如,在A-A’横截面的接触处形成孔隙;在B-B’ 横截面的接触处,在栅与接触之间对准精度不足可能导致失效;以及在C-C’横截面的接触开口处显然可能出现失效。
如图2所示,一旦工艺流程变的更加具体,对目标工艺流程中不同晶格的许多横截面视图进行系统检查,可使用自动建立和生成许多结构,这些结构可以覆盖大量的器件类型所使用的尖端工艺:n- 和p- 通道金属氧化物半导体(MOS)晶体管、嵌入式内存、输入/输出器件等。如果不能自动生成结构,则几乎不可能手动建立和模拟所需横截面视图。
为过滤危险晶格,计算机辅助设计技术(TCAD)工具可最多对代表晶格的截面通过最多150个工艺步骤对晶粒X进行系统检测,这几乎是手动所无法完成的。

图2.为过滤危险晶格,计算机辅助设计技术(TCAD)工具可最多对代表晶格的截面通过最多150个工艺步骤对晶粒X进行系统检测,这几乎是手动所无法完成的。
评论