高压变频技术在电弧炉除尘系统中的应用
1 概述
本文引用地址:https://www.eepw.com.cn/article/201808/387328.htm长期以来钢铁厂因其资源密集、能耗密集、生产规模大、物流吞吐量大等特点,被认为是烟尘排放量大、废弃物多、污染大的企业。而采用电弧炉炼钢是一些钢铁厂造成烟尘污染的主要来源之一。
电弧炉(简称电炉)主要是通过用废钢、铁合金和部分渣料进行配料冶炼,根据不同的钢种要求,可以接受高炭铬铁水和脱磷铁水,然后熔制出碳钢或不锈钢钢水供连铸用。电炉炼钢时产生的有害污染物主要是在电炉加料、冶炼、出钢三个阶段。电炉冶炼一般分为熔化期、氧化期和还原期,其中氧化期强化脱炭,由于吹氧或加矿石而产生大量赤褐色浓烟。在上述三个冶炼期中,氧化期产生的烟气量最大,含尘浓度和烟气温度最高。因此,电炉除尘系统是按照氧化期的最大烟尘排量进行设计的。电炉在冶炼过程中的粉尘主要通过炉顶烟道经沉降室沉积,水冷壁冷却后经除尘系统过滤排放;同时利用集尘罩将现场生产车间的粉尘和废气及时排走,以免污染环境和危及电炉周边工作人员的安全。因此,除尘风机是将烟气吸收排放的主要设备。一般情况下,在系统最大风量需求的基础上增加1.1耀1.3 倍的安全裕度进行除尘风机选型设计。整个炼钢过程中吹氧时期占30%耀35%,此时风机处于较高负荷运行,而其余时间则处于较低运行工况。但不论电炉处于哪一个运行阶段,除尘风机均全速运行,采用调节入口挡板开度来清理产生的粉尘,效率低、功率大、造成大量的电能浪费。随着市场竞争的不断加剧,节能降耗、提高生产效率成为企业发展提高竞争力的有效手段之一。
在上世纪90 年代开始使用的高压大功率变频调速技术则正是适应了市场的需求,在技术和应用领域上得到不断的进步和拓展,当时只是使用进口的高压变频器。进入21 世纪,随着我国科学技术的发展,自主研发的高压变频技术已广泛应用于电力、石油化工、矿山、冶金、给排水、机车牵引等领域。
太钢不锈钢股份有限公司某炼钢厂正是在这种状况下,对电炉除尘系统进行了高压变频技术改造。
2 系统技术方案研究
太钢不锈钢股份有限公司某炼钢厂的电炉为交流电弧炉。除尘器系统采用布袋式除尘器,设计过滤面积5 200 m2,最大除尘风量280 000 m3辕h。
该电炉的炼钢周期为70耀80 min,其中装料6%耀10%,送电熔化25%耀30%,吹氧30%耀35%,还原期15%耀20%,冲渣出钢6%耀8%。在不同的生产工艺阶段,电炉产生的烟气量和烟气温度不同,且差异较大。加料过程中,主要是装料时废钢及渣料产生的扬尘,需要的除尘风量不大,要求粉尘不扩散,不污染电炉周边工作环境为标准。送电过程中是原料送电拉弧加热,引发可燃废弃物燃烧产生废气。此时,电炉需要将炉料加热至熔化状态,要求烟尘能够及时排出,又不能过多的带走炉体热量以保证炼钢周期。而在吹氧期间,不仅要求除尘系统能够及时迅速的将废气和粉尘排走,又必须保证炉体有合适的吹炼温度,确保终点温度。因此,对除尘系统要求较高。进入还原期,吹氧告一段落,粉尘度再一次降低。在冲渣出钢时,主要排放物是冲渣产生的水蒸气和少量废气。
通过对冶炼工艺进行分析,电炉在炼钢过程的不同阶段对除尘风量的大小要求有明显的不同,以吹氧冶炼为最大,加料除尘为最低。鉴于电炉除尘系统中除尘风机的运行方式和设备特点,对除尘风机的控制系统制定了如下方案。
2.1 设备参数
除尘风机设备参数如表1 所列。
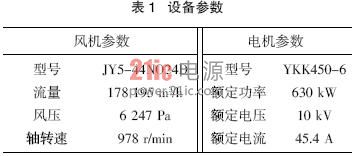
2.2 系统电气构成
根据现场生产工艺情况,选用成熟的高压变频器作为主件,该高压变频调速系统具有谐波含量小、功率因数高、编程灵活、操作方便、模块化结构、故障率低、免维护、易维修等特点。
除尘风机电气系统的主接线结构如图1 所示,10 kV电源通过母线段网侧高压开关QF 接入系统,采用多重化移相干式隔离变压器进行电源侧电气隔离,以减小对电网的谐波污染;变压器输出经功率柜逆变输出后直接驱动三相异步电动机,实现对除尘风量的控制。为保证除尘风机安全可靠运行,系统设计了工频/变频两套供电系统。
当系统变频运行时,断开隔离开关QS3,合隔离开关QS1、QS2,由变频器启停设备,实现对除尘风机的转速和风量控制。当变频装置出现故障时,系统切换至原工频运行方式,断开隔离开关QS1、QS2,合隔离开关QS3,直接启动风机,调节入口挡板控制风量。
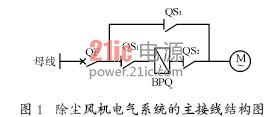
2.3 系统控制方案
由于不同工艺阶段的烟气温度有明显差异,因此温度的高低直接反映了电炉的运行工况。系统并没有采用检测电炉工作中粉尘浓度的方式来直接控制除尘风量,而是采集烟道温度作为系统调节的基本参量,通过非线性函数关系推导出不同运行工况下的除尘风量参与系统控制。从工程角度讲,温度变送器可以在恶劣的工业场合应用,其抗干扰能力强、工作稳定性好、控制精度高、安全可靠、免维护且价格便宜。而粉尘浓度检测装置有价格昂贵、稳定性差、故障率高、维护量大、现场检测点数据采集很难具有广泛代表性等缺点。基于上述原因,选用除尘烟道的烟气温度作为现场控制量。同时,以吹氧量和冷风门开度作为除尘风量的修整参量,从而提高系统响应速度,改善控制品质,达到良好的除尘效果,实现除尘风量自动控制,降低运行人员劳动强度,提高系统效率,达到最佳的节电效果。具体的控制逻辑如图2所示.
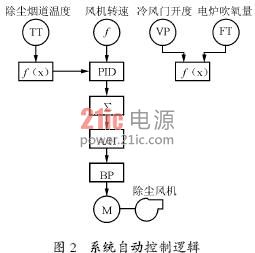
为了保证系统的可靠性,另外增加了除尘风量手动控制回路,对除尘风量的控制采用分段调速的方式由炉前操作台控制变频运行的频率点,从而实现不同运行工况下的风量调节。控制逻辑图如图3所示。
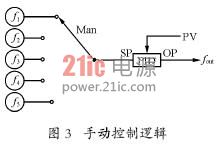
实践证明在设计了两套控制方案后大大提高了系统的实用性和可操作性,很好地满足了现场生产要求。同时,在改善现场工作环境,提高产品质量,降低吨钢能耗方面也起到了积极作用。
3 系统特点
1)除尘设备功耗随电炉炼钢生产工艺变负荷运行,提高了系统效率;实现了除尘系统的最佳工况运行,取得显著的节能效果。
2)大大降低了除尘系统负荷率,延长了除尘器、除尘风机、除尘电机、烟道等设备的使用寿命。
3)对降低炉内热量损失,合理控制过程温度,确保终点温度起到一定的作用。
4)对除尘系统进行变频改造,有助于改善炉内吹炼工况,缩短炼钢时间,提高钢产量改善出钢品质。
5)降低补炉期间的能耗和炉衬散热损失。
4 变频改造效益分析
为了对除尘系统变频改造后的效果进行评价,选取变频器投入前一个月和投入正常运行后一个月(保证投入前后各一个月的钢产量基本一致),对这两个月的设备实际使用和节电情况进行了测定和数据分析。
除尘系统变频改造前用电量数据如下(以2007 年12 月份为例)。
2007 年12 月钢产量为36 406 t,12 月1 日除尘风机电机功率表读数为1 838 460 kW·h,12月30日除尘风机电机功率表读数为2 118 580 kW·h,因此,12 月除尘风机工频运行时共消耗电量为(2 118 580-1 838 460)=280 120 kW·h,平均每天消耗电量为280 120 kW·h衣29天=9 659.3 kW·h。
除尘系统变频改造后用电量数据如下(以2008年4 月份为例)。
2008 年4 月钢产量36 416 t,2008 年4 月1日除尘风机电机功率表读数为2 899 520 kW·h,4月30日功率表读数为3 074 340 kW·h,因此,除尘系统变频器投用后,2008年4 月份共消耗电量为(3 074 340-2 899 520)=174 820 kW·h,平均每天消耗电量为174 820 kW·h衣29 天=6 028.3 kW·h。
根据以上数据测算,除尘系统变频器改造后平均每天节约电量为3 631 kW·h,节电率达到37.6%则每年节约电量为3 631 kW·h伊30 天伊12 月越1 307 160 kW·h,故每年可节约电费1 307 160 kW·h伊0.5 元/kW·h =65.4万元。
5 结语
在电弧炉除尘系统中应用高压变频调速技术不仅对改善现场生产状况、提高钢产量、降低电能消耗有着重要的意义,而且每年还可节约65万元左右的电费开支。同时对高压电机的启动起到了保护作用,降低了在启动电机时对电网的冲击。
评论