数控伺服技术在真空成型机自控系统中的应用
真空成型机是一种采用热成型工艺对冰箱内胆进行加工生产的大型设备。成型机的设计和制造在它的生产涉及了控制理论、热成型工艺学、材料学、红外辐射、热传导、总线通信、气压液压传动以及机械传动等多学科的知识,成型机是多学科知识交叉和融合的集中体现。长期以来,我国塑料加工成型机的技术水平一直落后于日本、美国、德国等国家。虽然我国也能进行成型机的设计和生产,但是在设备的自动化程度、安全性、稳定性和速度等指标上还远达不到欧美日等国家的水平,这使得国内高端成型机的市场长期被几大国外品牌所占据,造成了大量的外汇开支。
针对当前我国各行各业虽然比较齐全,但是设计水平还不是很高的现状,国家提出了建设创新型社会的号召,鼓励对于国外先进技术的消化吸收和再创新,以改变我国各行业大而不强的面貌。本项目的实施和本文的最终完成就是在这种大环境下进行的。本文重点并详细介绍了真空成型机控制系统中传动部分的控制方法。
第二章工艺流程及控制要求
真空成型机是对薄软非金属材料(主要是热塑性塑料)用模具进行热成型加工的大型设备。在电冰箱生产线,主要用于生产电冰箱和半导体电子冰箱的内胆(冷藏室和冷冻室箱体),是冰箱生产线上的重要设备。由于真空成型机体型庞大、工艺复杂,并且涉及到电气、机械、气压与液压传动等多学科的知识,使得成型机具有投资大、控制难度高、维护要求高等特点。目前高质量的真空成型机主要依赖进口。
如图1所示为四工位真空成型机。
四工位真空成型机,“四工位”我们可以理解为四个工段,即一张片材要先后经过四个工段的加工后才能得到制品,也就是冰箱内胆。这四个工段分别是

下面我将分别介绍一下这四个工段,以使读者对四工位真空成型机有一个大概的了解。
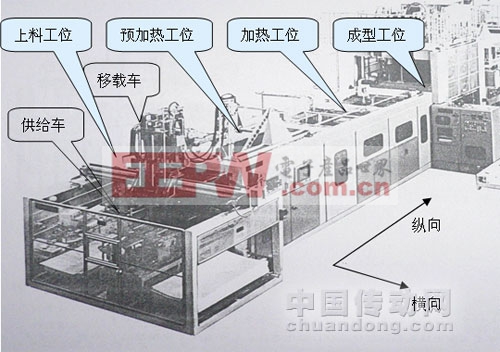
图1四工位真空成型机图样
上料工位
上料工位用于存放设备进行生产所用的片材(主要是ABS和HIPS两种热塑性材料,加工尺寸最大为1860*900mm,最小为1100*535mm),并按照一定的生产工序要求,将片材送到下一工位:预加热工位。上料工位主要包括两部分,一是移载车,二是供给车。移载车做横向运动,用于将分布在设备两侧的片材放置到供给车上;供给车做纵向运动,用于将片材送到下一工位:预加热工位。
预加热工位
预加热工位用来对从上料工位运来的,待加工成型的片材进行预加热,以使片材能得到初步软化,并节省最终加热时间,见图2(a)。对片材加热所用加热器为浅野研究所开发出的快速反应加热器(PAT),这种加热器以红外加热瓦为基本单位,采取了远红外线辐射的方式对塑料进行加热,不需热传介质传递,热效率良好,并可以根据加热状况和控制条件随时调整发热量,节约电能。
在预加热工位,加热是由上、下加热器共同作用的,上、下加热器各有98块加热瓦(0.4kw),功率分别为39.2kw。加热工位片材在预加热工位得到了初步的加热,并有所软化,在经过一定的加热时间后,片材进入加热工位。在这里,片材在上、下两块加热器的共同作用下,得到更进一步的、深度的加热。通过这种深度的加热,可以使片材最终的软化程度达到成型的要求,这时,片材的中间部位软化最为严重,这个区域会向下弯曲,使得片材形状呈碗形,参见图2(b)。
加热工位所用加热器与预加热工位相同,只是加热瓦数量比预加热工位更多,功率也比预加热工位更大。在加热工位,上、下加热器分别有144块加热瓦,功率分别为57.6kw。
3.成型定位
加热工位的下一个工段是成型工位。片材在经过预加热工位和加热工位的加热,并且片材的软化程度达到成型规定的要求后,将会在成型工位处得到加工,并最终得到冰箱内胆制品。
成型工位部分主要包括上、下平台,凸、凹模具,以及配套的真空、压空、冷却系统等。其中,凸、凹模具能互相吻合,凸模具固定在上平台,凹模具固定在下平台上,平台的移动靠液压系统来控制,模具随着平台的运动而运动。当软化后的片材移动到成型工位并固定后,上、下平台相向运动,下平台首先与片材接触并形成一个密闭的空间,并抽真空,使得片材进一步弯曲,对片材起到预拉伸的作用,当上平台也与片材接触并形成密闭空间后,抽真空,同时下平台改为充入压缩气体,使片材紧贴在模具上,最后冷却,脱模,得到内胆制品。具体成型过程可参见图2(c)(d)(e)。
2.3控制要求
1.设备具有手动和自动两种状态。
手动状态下,操作人员可以通过按钮来控制成型机的动作,如移载车前进、
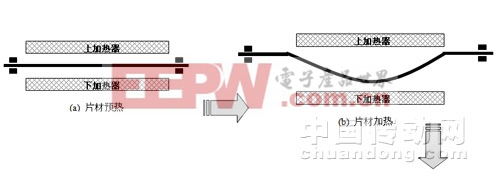
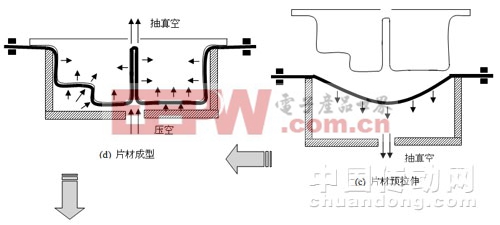
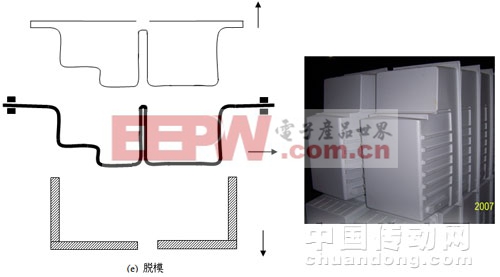
图2片材成型过程示意图
后退;供给车前进、后退;平台上升、下降等,手动按钮用于设备的调试,以及某些紧急情况下的应急处理。
自动状态是成型机控制系统的主要运行方式,在自动状态下,片材的吸取、加热、成型完全依靠控制器按照设定的程序来运行,不需要人工干预,即一种完全自动化流水线的生产状态,操作人员只需在成型工位处将不断成型的制品取出便可。
2.设备具有正常停止和紧急停止功能
因为成型机在运行期间采用循环工作方式,只有在工作结束时才能停止,这时,设备要能根据控制器的命令自动停止系统运行;而紧急停止则用于紧急情况的处理,当这一功能生效时,加热器、平台等成型机所有部件立即停止运行。
3.设备要有报警功能,当设备发生联锁故障或是其它严重错误时,系统要具有声光报警,提醒操作人员发生故障,并能用一定的故障码来表示一定的故障。
4.通讯系统应该满足如下要求:
数字量采集周期0.1s;
模拟量采集周期0.2s;
控制命令响应时间:①控制命令回答响应时间
②接受执行命令到执行控制的响应时间1s;
③报警或事件产生到画面显示和发出的响应时间0.5s。
第三章数控伺服系统设计
真空成型机包括四个工位,即上料、预加热、加热、成型。每一工位片材或成品的移动是靠横贯于这四个工位的两条链条带动来实现的,当需要片材往前移动时,由链条的链齿夹住片材向前运动。在生产中,链条的移动需要满足一定的控制要求,如链条的控制设备起动及低速运行时要具有较大转矩,过载能力强,具有较宽的调速范围,而且要响应速度快,能急起急停,准确定位等。一般通用型的变频器,即使加编码器构成闭环控制,也不能完全满足上述要求。在这种情况下,采用伺服控制是最佳的选择,由于伺服电机的材料、结构和加工工艺要远远高于一般的交流异步电机,伺服控制系统输出转矩大,过载能力强,稳定性好,控制精度高,响应快,伺服系统能较好地满足系统控制要求。在本系统中选择的伺服系统是FANUCPowerMate-A-20S,其中,PowerMate-A指的是伺服控制器型号,20S指的是伺服电机型号,即FANUC公司S系列交流伺服电机中的20S子系列。
严格意义上来说,在本系统中,链条的控制是靠数控系统来完成的,伺服系统只是数控系统的一部分,它负责将数控系统与机床(指链条)连接起来,并准确地执行CNC系统发来的运动命令,按照要求驱动机床(链条)。因此,如果说CNC系统是数控系统的“大脑”,那么,伺服驱动部分便是数控系统的“四肢”,执行机构。下面我将结合实际系统简要介绍数控和伺服方面的知识。
数控技术,简称数控(NumericalControl—NC),是利用数字化信息对机械运动及加工过程进行控制的一种方法,由于现代数控都采用了计算机进行控制,因此,也可称为计算机数控(ComputerizedNumericalControl—CNC),而用来实现数字化信息控制的硬件和软件的整体成为数控系统(NumericalControlSystem),数控系统是数控机床的核心部分,数控机床在数控系统的控制下,自动地按给定的程序进行机械零件的加工,在本系统中,表现为链条在数控系统的控制下,按照要求在合适的时间,以一定的速度前进或后退。
数控系统由用户程序、输入输出设备、计算机数控装置(CNC)、可编程控制器(PMC)、主轴驱动装置和进给驱动装置、位置检测装置等组成,其中,数控装置(CNC)是数控系统的核心。如图3所示为数控系统基本组成。
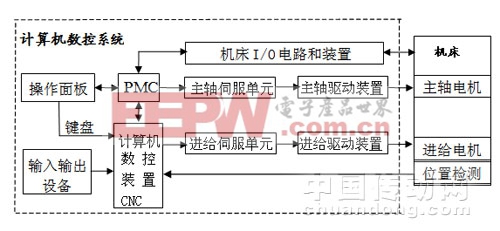
图3数控系统基本组成
3.1数控装置CNC
从自动控制的角度来看,数控系统是一种位置(轨迹)控制系统,其本质上是以多执行部件(各运动轴)的位移量为控制对象并使其协调运动的自动控制系统,而CNC则是数控系统的中央控制器,对于我们的数控系统来说,FANUCPowerMate-A便是系统的CNC,只不过PowerMate-A除了包含狭义上的数控装置(CNC)外,还将伺服放大器、PMC等集成在了一起,可见图3所示。
伺服电机相关文章:伺服电机工作原理
评论